Unlocking Industrial Communication: A Comprehensive Guide to RS-485
In the realm of industrial automation, efficient and reliable communication is paramount. Among the various communication protocols, RS-485 stands out as a robust and versatile solution for connecting devices over long distances. This article delves into the intricacies of RS-485, empowering professionals with a thorough understanding of its principles, benefits, applications, and implementation.
What is RS-485?
RS-485, or Recommended Standard 485, is a serial communication protocol that enables multiple devices to communicate over a single twisted-pair wire. It employs differential signaling to transmit data, ensuring exceptional noise immunity and reducing the impact of electrical interference.
Key Features of RS-485
-
Half-duplex communication: Data flows in both directions, but not simultaneously.
-
Multi-drop topology: Supports multiple devices connected to a single bus.
-
Long range: Transmission distances can reach up to 1,200 meters at low data rates (9.6 kbps).
-
High noise immunity: Differential signaling provides excellent rejection of common-mode noise and interference.
-
Low power consumption: RS-485 transceivers typically consume minimal power, making it suitable for battery-powered devices.
Benefits of Using RS-485
-
Scalability: Enables the connection of multiple devices to a single bus, facilitating the creation of complex networks.
-
Extended range: Long transmission distances allow for communication over wider areas, reducing the need for repeaters or intermediate devices.
-
High reliability: Differential signaling and twisted-pair wiring ensure reliable data transmission in harsh industrial environments.
-
Cost-effectiveness: RS-485 transceivers are relatively inexpensive, making it an affordable solution for connecting devices.
-
Easy implementation: The simple two-wire design simplifies installation and maintenance.
Applications of RS-485
RS-485 finds widespread application in a variety of industrial settings, including:

-
Industrial automation: Connecting sensors, actuators, and controllers in manufacturing environments.
-
Building management systems: Controlling lighting, heating, and other systems in commercial and residential buildings.
-
Transportation systems: Communicating between vehicle components and roadside infrastructure.
-
Medical equipment: Connecting medical devices to monitors and central systems.
-
Remote monitoring and control: Enabling communication with devices in remote locations.
Implementation of RS-485
Wiring Configuration
RS-485 utilizes a two-wire twisted-pair configuration. The two wires are designated as A and B, and the data is transmitted differentially between them.
Termination
To prevent signal reflections and maintain signal integrity, termination resistors must be connected to the ends of the RS-485 bus. Typically, 120-ohm resistors are used.
Communication Parameters
The following communication parameters must be established for RS-485 networks:
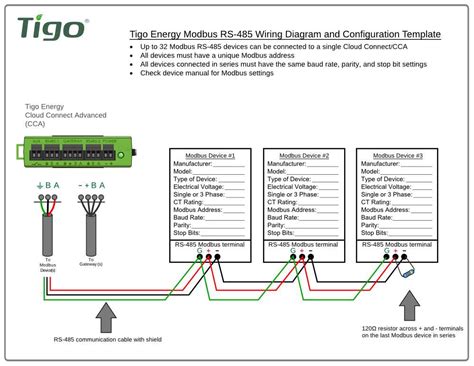
-
Baud rate: The speed at which data is transmitted, ranging from 300 bps to 10 Mbps.
-
Data format: The number of data bits, stop bits, and parity bit.
-
Protocol: The underlying communication protocol used, such as Modbus or ASCII.
Troubleshooting RS-485 Networks
Common troubleshooting techniques for RS-485 networks include:

-
Signal level measurement: Verifying that the signal levels are within the specified range.
-
Cable continuity test: Ensuring that the twisted-pair wires are properly connected and not broken.
-
Grounding verification: Confirming that all devices are properly grounded to eliminate common-mode noise.
-
Bus monitoring: Using an oscilloscope or logic analyzer to monitor the RS-485 bus for errors or abnormal behavior.
Case Studies
Example 1: Industrial Automation System
In a manufacturing plant, RS-485 is used to connect sensors, actuators, and controllers in a multi-drop topology. The extended range of RS-485 allows for communication over the large manufacturing floor, while the high noise immunity ensures reliable operation in the noisy environment.
Lessons Learned:
- RS-485 provides a cost-effective and reliable solution for industrial automation applications.
- Proper wiring and termination are crucial for maintaining signal integrity.
Example 2: Building Management System
In a commercial building, RS-485 is employed to connect lighting, heating, and other systems to a central control panel. The scalability of RS-485 enables the integration of multiple devices into a single network, while the easy implementation simplifies maintenance and upgrades.
Lessons Learned:
- RS-485 facilitates the creation of complex building management systems.
- The low power consumption of RS-485 is beneficial for battery-powered devices such as wireless sensors.
Example 3: Remote Telemetry System
In a remote monitoring application, RS-485 is used to transmit data from sensors located in a remote area to a central monitoring station. The long range of RS-485 enables communication over distances of several kilometers without the need for repeaters.
Lessons Learned:
- RS-485 is an effective communication solution for remote monitoring and control applications.
- Differential signaling ensures reliable data transmission even in harsh environmental conditions.
Effective Strategies for Implementing RS-485 Networks
-
Use quality cables and connectors: Invest in high-quality twisted-pair cables and connectors to ensure signal integrity and reduce errors.
-
Properly terminate the bus: Install 120-ohm termination resistors at the ends of the RS-485 bus to prevent signal reflections.
-
Ground all devices: Ensure that all devices connected to the RS-485 bus are properly grounded to eliminate common-mode noise.
-
Limit the number of devices on the bus: The maximum number of devices on an RS-485 bus is typically limited to 32, depending on the baud rate and cable length.
-
Monitor the bus traffic: Use a logic analyzer or oscilloscope to monitor the RS-485 bus for errors or abnormal behavior.
Step-by-Step Approach to Implementing RS-485 Networks
-
Define the communication parameters: Determine the baud rate, data format, and protocol to be used on the RS-485 bus.
-
Wire the network: Install twisted-pair cables and connect the devices to the bus using proper connectors.
-
Terminate the bus: Install 120-ohm termination resistors at the ends of the bus.
-
Ground all devices: Ensure that all devices connected to the bus are properly grounded.
-
Configure the devices: Set the communication parameters on each device to match the defined values.
-
Test the network: Verify the functionality of the network by sending and receiving test messages.
Comparison of RS-485 with Other Serial Protocols
Feature |
RS-485 |
RS-232 |
RS-422 |
Range |
Up to 1,200 m |
Up to 15 m |
Up to 1,200 m |
Noise Immunity |
Excellent |
Good |
Very Good |
Baud Rate |
Up to 10 Mbps |
Up to 115.2 kbps |
Up to 10 Mbps |
Topology |
Multi-drop |
Point-to-point |
Point-to-point |
Devices |
Up to 32 |
1 |
10 |
Cost |
Moderate |
Low |
Moderate |
Conclusion
RS-485 is a versatile and reliable communication protocol that provides a robust and cost-effective solution for connecting devices in a wide range of industrial applications. Its long range, high noise immunity, and scalability make it an ideal choice for applications requiring efficient and reliable data exchange over extended distances. By understanding the principles, benefits, and implementation strategies of RS-485, professionals can effectively deploy this technology to enhance the performance and reliability of their systems.