The Ultimate Guide to Sensor Pressure Transducers: Unlocking Precision in Pressure Measurement
Introduction
In the realm of industrial automation, precision is paramount. Sensor pressure transducers play a pivotal role in ensuring accurate measurement of pressure, a critical parameter in various manufacturing, energy, and environmental processes. This comprehensive guide delves into the intricacies of sensor pressure transducers, exploring their design, working principles, applications, and practical considerations.
What is a Sensor Pressure Transducer?
A sensor pressure transducer is a device that converts pressure into an electrical signal. It consists of a sensing element, a signal conditioner, and an output device. The sensing element, usually a diaphragm or a bourdon tube, detects changes in pressure and generates a mechanical response. The signal conditioner amplifies and converts this mechanical response into a proportional electrical signal. The output device then transmits this signal for further processing or display.
Types of Sensor Pressure Transducers
Sensor pressure transducers are classified into several types based on various characteristics:
-
Diaphragm Transducers: Utilizing a flexible diaphragm as the sensing element, diaphragm transducers are suitable for measuring pressure in liquids and gases.
-
Bourdon Tube Transducers: Employing a curved metal tube that deforms under pressure, bourdon tube transducers offer high accuracy and stability.
-
Capacitive Transducers: Detecting pressure changes based on the capacitance variations of a sensing element, capacitive transducers provide highly sensitive measurements.
-
Piezoresistive Transducers: Using semiconductor materials that exhibit changes in resistance under pressure, piezoresistive transducers offer a wide operating range and high sensitivity.
-
Strain Gauge Transducers: Incorporating strain gauges to measure the deformation of a sensing element, strain gauge transducers are suitable for harsh environments.
Working Principles of Sensor Pressure Transducers
The working principle of a sensor pressure transducer depends on its specific design:

Diaphragm Transducers:
- A diaphragm separates the process fluid from the sensing element.
- Pressure changes cause the diaphragm to deflect, generating a mechanical signal.
- The signal conditioner amplifies and converts the mechanical signal into an electrical signal.
Bourdon Tube Transducers:
- A curved metal tube is connected to the pressure source.
- Pressure changes cause the tube to deform, rotating a pointer or generating a cam movement.
- The displacement or cam movement is converted into an electrical signal by the signal conditioner.
Capacitive Transducers:
- A sensing element forms one plate of a capacitor.
- Pressure changes alter the spacing between the plates, affecting the capacitance.
- The signal conditioner measures the capacitance changes and converts them into an electrical signal.
Piezoresistive Transducers:
- A semiconductor element is bonded to a sensing diaphragm.
- Pressure changes cause the diaphragm to deform, changing the resistance of the semiconductor element.
- The signal conditioner amplifies and converts the resistance changes into an electrical signal.
Applications of Sensor Pressure Transducers
Sensor pressure transducers have a wide range of applications across various industries:
-
Industrial Automation: Monitoring pressure in hydraulic systems, pneumatic circuits, and process control systems.
-
Medical Devices: Measuring blood pressure, respiratory pressure, and anesthesia monitoring.
-
Automotive Industry: Monitoring tire pressure, brake pressure, and engine performance.
-
Aerospace and Defense: Measuring altitude, airspeed, and fuel pressure in aircraft and spacecraft.
-
Environmental Monitoring: Monitoring atmospheric pressure, water pressure, and soil pressure.
Benefits of Sensor Pressure Transducers
-
High Accuracy: Reliable and precise measurements of pressure, ensuring accurate control and monitoring.
-
Wide Range: Suitable for measuring pressures from low vacuums to high pressures, supporting various applications.
-
Compact Design: Designed to be small and lightweight, allowing for easy integration into existing systems.
-
Rugged Construction: Built to withstand harsh environments, ensuring reliability in demanding conditions.
-
Low Maintenance: Requiring minimal maintenance, reducing downtime and operational costs.
Considerations for Selecting a Sensor Pressure Transducer
Selecting the right sensor pressure transducer for a specific application requires careful consideration of several factors:
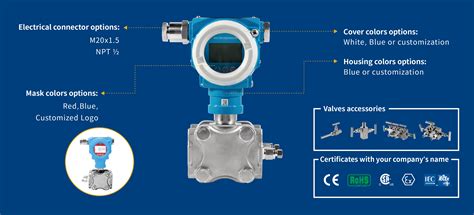

-
Pressure Range: The maximum and minimum pressure that the transducer can measure accurately.
-
Accuracy: The percentage error between the measured pressure and the actual pressure.
-
Measurement Type: The type of pressure (gauge, absolute, or differential) that the transducer can measure.
-
Output Signal: The type of output signal (voltage, current, or digital) required for the application.
-
Environmental Conditions: The temperature range, humidity, and vibration levels that the transducer will be exposed to.
Tips and Tricks for Using Sensor Pressure Transducers
-
Calibration: Regularly calibrate the transducer to ensure accuracy and reliability.
-
Overpressure Protection: Use overpressure protection devices to prevent damage from excessive pressure.
-
Proper Installation: Ensure proper installation to minimize measurement errors and maintain long-term performance.
-
Regular Maintenance: Routinely inspect and clean the transducer to prevent contamination and ensure optimal performance.
-
Consider Redundancy: Use multiple transducers for critical applications to provide redundancy and improve reliability.
How to Step-by-Step Approach
-
Define the Pressure Measurement Requirements: Determine the pressure range, accuracy, and measurement type required for the application.
-
Select the Transducer: Choose the appropriate transducer based on the specified requirements, considering its design, performance, and environmental compatibility.
-
Install the Transducer: Follow the manufacturer's instructions for proper installation, ensuring correct orientation and appropriate mounting techniques.
-
Calibrate the Transducer: Perform calibration to ensure accuracy and traceability of the measurements.
-
Monitor and Maintain the Transducer: Regularly monitor the transducer's performance and implement proper maintenance practices to ensure long-term reliability.
Why Sensor Pressure Transducers Matter
Sensor pressure transducers play a crucial role in industries where precision, reliability, and efficiency are paramount. They enable accurate pressure measurement, contributing to:
-
Improved Safety: Ensuring proper operation of pressure systems, preventing accidents and protecting personnel.
-
Efficient Process Control: Enabling precise monitoring and control of pressure parameters, optimizing processes and increasing productivity.
-
Enhanced Product Quality: Ensuring proper functioning of pressure-sensitive equipment, leading to consistent and high-quality products.
-
Environmental Protection: Monitoring and controlling pressure in environmental systems, reducing pollution and preserving natural resources.
-
Increased Profitability: Reducing downtime, improving efficiency, and minimizing waste, resulting in increased profitability.
Pros and Cons of Sensor Pressure Transducers
Pros:
- High accuracy and precision
- Wide range of pressure measurement
- Compact and rugged designs
- Excellent durability and reliability
Cons:
- Can be expensive compared to other pressure measurement methods
- May require calibration and maintenance
- May be affected by environmental conditions, such as temperature and vibration
Comparative Analysis of Sensor Pressure Transducers
The table below compares different types of sensor pressure transducers based on their characteristics:
Type |
Sensing Element |
Output Signal |
Accuracy |
Pressure Range |
Advantages |
Disadvantages |
Diaphragm |
Diaphragm |
Voltage or current |
±0.5% FSO |
Vacuum to thousands of psi |
Compact, low cost |
Temperature-sensitive |
Bourdon Tube |
Curved metal tube |
Mechanical linkage |
±1% FSO |
Low pressure to several thousand psi |
Rugged, durable |
Limited accuracy |
Capacitive |
Capacitive plates |
Voltage or current |
±0.1% FSO |
Vacuum to hundreds of psi |
High sensitivity |
Temperature-sensitive |
Piezoresistive |
Semiconductor element |
Voltage or current |
±0.1% FSO |
Low pressure to thousands of psi |
Compact, wide range |
Strain-sensitive |
Table 1: Comparison of Sensor Pressure Transducer Types
Application Examples of Sensor Pressure Transducers
-
Industrial Automation: Measuring pressure in hydraulic systems of machine tools, robots, and automated assembly lines.
-
Medical Devices: Monitoring blood pressure, respiratory pressure, and CPAP (continuous positive airway pressure) devices.
-
Automotive Industry: Measuring tire pressure, fuel pressure, and brake pressure in vehicles.
-
Aerospace and Defense: Measuring altitude, airspeed, and fuel pressure in aircraft and missiles.
-
Environmental Monitoring: Measuring atmospheric pressure, water pressure, and soil pressure for weather forecasting and environmental monitoring.
Table 2: Applications of Sensor Pressure Transducers
Market Trends and Future Prospects
The global sensor pressure transducer market is projected to grow significantly in the coming years, driven by increasing demand from industries such as industrial automation, medical devices, and automotive. Technological advancements, such as wireless connectivity and miniaturization, are expected to further drive market growth.
Table 3: Market Trends and Future Prospects of Sensor Pressure Transducers
Year |
Market Value |
Growth Rate |
2021 |
USD 10.5 billion |
5.5% |
2022 |
USD 11.2 billion |
6.3% |
2027 |
USD 16.5 billion |
7.2% (estimated) |
Inspirational Quotes
- "Precision is the mother of all virtues." - Aristotle
- "The only way to do great work is to love what you do." - Steve Jobs
- "Measurement is the first step that leads to control and eventually to improvement. If you can't measure something, you can't understand it. If you can't understand it, you can't control it. If you can't control it, you can't improve it." - H.