A Comprehensive Guide to Lock Nuts: Ensuring Secure Connections in Machine Applications
Lock nuts are an essential component in a wide range of mechanical assemblies, ensuring the reliability and safety of bolted connections. They play a crucial role in preventing unintentional loosening due to vibrations, dynamic loads, or other environmental factors. This article provides an in-depth exploration of lock nuts, covering their types, applications, advantages, disadvantages, and best practices for their use.
Types of Lock Nuts
Lock nuts come in various designs, each with unique characteristics suited for specific applications. Some of the most common types include:
-
Nylon-Insert Lock Nuts: Featuring a nylon ring embedded in the threads, these nuts provide a locking mechanism that prevents loosening by gripping the mating bolt.
-
Split-Beam Lock Nuts: These nuts have a split beam construction that creates spring tension against the bolt threads, effectively locking them in place.
-
All-Metal Lock Nuts: Made entirely of metal, these nuts utilize various mechanisms, such as deformed threads or Belleville washers, to generate a locking force.
-
Self-Locking Nuts: These nuts incorporate a built-in locking mechanism, such as a plastic insert, that provides resistance to loosening without the need for additional hardware.
Materials and Standards
Lock nuts are typically manufactured from high-strength steel, such as alloy steel or stainless steel, to ensure durability and resistance to corrosion. They are manufactured according to various industry standards, including:
-
ASTM International (ASTM): ASTM A563, ASTM A564, ASTM F810
-
International Organization for Standardization (ISO): ISO 4032, ISO 7042, ISO 7043
-
American National Standards Institute (ANSI): ANSI B18.16.4
Applications of Lock Nuts
Lock nuts find extensive use in a wide array of industries and applications, including:
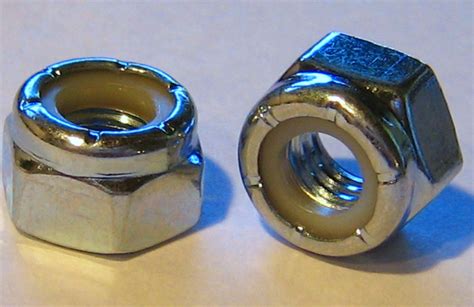

-
Automotive: Engine components, suspension systems, brakes
-
Industrial Machinery: Heavy equipment, conveyor belts, pumps
-
Construction: Structural steel connections, bridges, buildings
-
Aerospace: Aircraft engines, landing gear, hydraulic systems
-
Military: Weapons, vehicles, electronic equipment
Benefits of Using Lock Nuts
Incorporating lock nuts into mechanical assemblies offers numerous benefits:
-
Prevents Unintentional Loosening: Ensures that bolted connections remain secure, even under dynamic loads and vibrations.
-
Reduces Maintenance Costs: Eliminates the need for frequent tightening, reducing downtime and maintenance expenses.
-
Improves Safety: Prevents catastrophic failures by ensuring that critical components stay securely fastened.
-
Enhances Reliability: Ensures the proper functioning of equipment and systems by maintaining secure connections.
Disadvantages of Using Lock Nuts
While lock nuts provide significant advantages, they also have some potential drawbacks:
-
Increased Cost: Lock nuts can be more expensive than standard nuts due to their more complex design and manufacturing.
-
Incompatibility: Some lock nuts may not be suitable for use with certain types of bolts or in specific applications.
-
Damage to Threads: Overtightening lock nuts can damage the threads on the bolt or the nut itself.
-
Limited Reusability: Some lock nuts are not designed to be reused multiple times, which can increase replacement costs.
How to Choose the Right Lock Nut
Selecting the appropriate lock nut for a given application requires careful consideration of several factors:

-
Application: Identifying the industry and specific use case where the lock nut will be employed.
-
Load Requirements: Determining the dynamic and static loads that the connection will experience.
-
Environmental Conditions: Considering the operating temperature, humidity, corrosion resistance, and other environmental factors.
-
Material Compatibility: Ensuring that the lock nut material is compatible with the mating bolt and the surrounding environment.
-
Reusability Requirements: Establishing whether the lock nut will need to be reused in the future.
Common Mistakes to Avoid
To ensure the optimal performance and safety of lock nuts, it is essential to avoid common mistakes:
-
Overtightening: Excessive tightening can damage the threads and reduce the locking effectiveness.
-
Using Incompatible Lock Nuts: Selecting lock nuts that are not compatible with the bolt or application can lead to failure.
-
Reusing Single-Use Lock Nuts: Some lock nuts are not designed to be reused and may not provide adequate locking strength if reused.
-
Mixing Lock Nut Types: Using different types of lock nuts on the same connection can compromise reliability.
-
Ignoring Maintenance: Regularly inspecting and tightening bolted connections, including lock nuts, is crucial for maintaining their functionality.
Step-by-Step Approach to Installing Lock Nuts
Installing lock nuts correctly is essential for ensuring their effectiveness and longevity:
-
Prepare the Bolt: Clean the threads of the bolt to remove any dirt or debris.
-
Apply Lubrication: Apply a light coat of lubricant to the bolt threads to reduce friction during installation.
-
Place the Lock Nut: Position the lock nut on the bolt by hand, ensuring that it is the correct size and type.
-
Tighten the Lock Nut: Use a wrench or torque wrench to tighten the lock nut to the specified torque value.
-
Inspect the Installation: Visually inspect the connection to ensure that the lock nut is securely tightened and properly seated.
Table 1: Torque Values for Lock Nuts
Lock Nut Type |
Torque (ft-lb) |
Nylon-Insert |
15-25 |
Split-Beam |
20-30 |
All-Metal |
40-60 |
Table 2: Lock Nut Selection Criteria
Factor |
Consideration |
Application |
Industry, specific use case |
Load Requirements |
Dynamic and static loads |
Environmental Conditions |
Temperature, humidity, corrosion |
Material Compatibility |
Matching with bolt and environment |
Reusability |
Need for future reuse |
Table 3: Common Lock Nut Applications
Application |
Lock Nut Type |
Automotive Engine |
Nylon-Insert, Split-Beam |
Industrial Machinery |
All-Metal, Self-Locking |
Construction Steel Connections |
Split-Beam |
Aerospace Landing Gear |
All-Metal, Self-Locking |
Military Weapons |
All-Metal, Split-Beam |
Conclusion
Lock nuts play a vital role in ensuring the reliability, safety, and proper functioning of bolted connections in a wide range of applications. By understanding the different types, materials, applications, advantages, and limitations of lock nuts, and by following best practices for their installation and maintenance, engineers and technicians can design and assemble secure and durable mechanical assemblies.