**Lichtbogenschweißen: A Comprehensive Guide to Arc Welding**
Introduction
Lichtbogenschweißen, also known as arc welding, is a versatile and widely used joining process that utilizes an electric arc to melt the base metal and the filler material together. It is a highly efficient and effective method for permanently bonding metals, offering numerous advantages over other welding techniques.
Advantages of Arc Welding
-
High welding speed: Arc welding allows for rapid joining of metal components, making it suitable for high-volume production environments.
-
Strong welds: The electric arc generates intense heat, resulting in strong and durable welds that can withstand significant loads and stresses.
-
Versatile: Arc welding can be used on a wide range of metals, including steel, aluminum, and stainless steel. It is also adaptable to various joint configurations and welding positions.
-
Cost-effective: Compared to other welding methods, arc welding is relatively inexpensive, as it does not require specialized equipment or a large investment in consumable materials.
Types of Arc Welding Processes
There are several types of arc welding processes, each with its unique characteristics and applications:
1. Shielded Metal Arc Welding (SMAW)
-
Description: Also known as stick welding, SMAW uses a consumable electrode that melts and forms a slag layer to protect the weld pool from contamination.
-
Advantages: Simple and cost-effective, suitable for outdoor welding and limited-access areas.
-
Disadvantages: Slower than other processes, produces more spatter and slag.
2. Gas Metal Arc Welding (GMAW)
-
Description: Also known as MIG welding, GMAW utilizes a continuously fed metal wire as the electrode, shielding the weld pool with an inert or active gas.
-
Advantages: Fast, efficient, and produces high-quality welds with minimal spatter.
-
Disadvantages: Requires a separate gas supply, can be sensitive to wind.
3. Gas Tungsten Arc Welding (GTAW)
-
Description: Also known as TIG welding, GTAW uses a non-consumable tungsten electrode and an inert gas to shield the weld pool.
-
Advantages: Produces precise and aesthetically pleasing welds, ideal for thin materials and critical applications.
-
Disadvantages: Slower and more skill-intensive than other processes.
Selection of Welding Electrodes
The selection of the appropriate welding electrode is crucial for the quality and performance of arc welded joints. Factors to consider include:
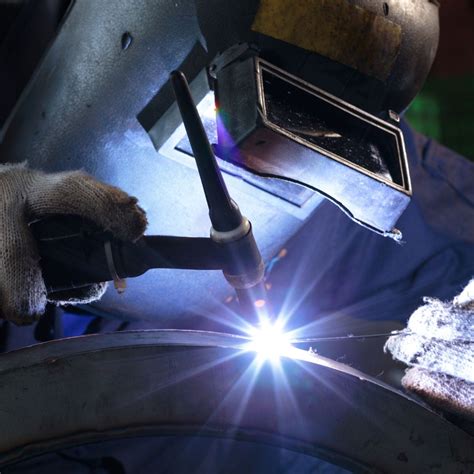
-
Material composition: The electrode should match the base metal composition to ensure compatibility and avoid weld defects.
-
Diameter: The electrode diameter affects the heat input and weld penetration depth.
-
Coating: The coating on the electrode provides shielding, stabilizes the arc, and influences weld properties.
Welding Safety
Arc welding involves significant hazards, including electric shock, arc flash, fumes, and molten metal. To ensure a safe work environment, follow these essential safety precautions:

- Wear proper protective clothing, including a welding helmet, gloves, and fire-resistant clothing.
- Use ground clamps to prevent electric shock.
- Ventilate the welding area to remove hazardous fumes.
- Keep the welding environment clean and organized to prevent tripping hazards.
Applications of Arc Welding
Arc welding is widely used in various industries and applications, including:
-
Automotive: Fabrication of car bodies, chassis, and exhaust systems.
-
Construction: Assembly of structural steel, bridges, and pipelines.
-
Manufacturing: Production of machinery, appliances, and electronic components.
-
Shipbuilding: Hull construction, deck plating, and repairs.
-
Repair and maintenance: Overhauling vehicles, equipment, and buildings.
Benefits of Arc Welding Automation
Automation of arc welding processes offers numerous benefits for businesses and manufacturers:
-
Increased productivity: Automated welding machines can operate 24/7, reducing production times and increasing output.
-
Consistent quality: Robots can ensure consistent weld parameters and reduce the likelihood of human error.
-
Improved safety: Removing humans from the welding environment reduces the risk of arc flash, fumes, and burn injuries.
-
Reduced labor costs: Automation eliminates the need for highly skilled welders, reducing labor expenses.
Troubleshooting Common Arc Welding Problems
Arc welding processes can encounter various issues that can affect the quality of welds. Common problems include:

-
Porosity: Caused by trapped gases within the weld, resulting in voids and weakened welds.
-
Cracking: Occurs due to excessive stress or incorrect welding techniques, leading to brittle welds.
-
Undercut: A groove formed along the edges of the weld due to insufficient penetration.
-
Arc instability: Fluctuating arc characteristics can cause uneven welds and poor fusion.
Case Studies and Success Stories
Story 1: A manufacturing company implemented automated arc welding robots to increase production capacity for automotive parts. The robots increased output by 30% while reducing defect rates by 50%.
Story 2: A shipbuilding yard adopted GMAW technology for hull assembly. The faster welding speed and improved weld quality enabled the yard to complete projects in 25% less time.
Story 3: A construction firm utilized GTAW for welding thin-walled stainless steel pipes in a cleanroom environment. The precision of GTAW ensured minimal contamination and met stringent industry standards.
What We Learn from These Stories
These case studies demonstrate the significant benefits of arc welding, including:
- Increased productivity and efficiency
- Improved weld quality and consistency
- Reduced labor costs and production time
- Enhanced safety and reduced risk of human error
Effective Strategies for Successful Arc Welding
To achieve optimal results from arc welding, consider these effective strategies:
-
Proper equipment maintenance: Regularly maintain welding machines and accessories to ensure reliable operation.
-
Skilled welders: Invest in training and certification of welders to ensure proficiency and adherence to best practices.
-
Adequate ventilation: Implement effective ventilation systems to remove welding fumes and protect workers' health.
-
Weld inspection and testing: Implement quality control measures to inspect and test welds for defects and meet industry standards.
Frequently Asked Questions
1. What is the difference between SMAW, GMAW, and GTAW?
-
SMAW: Consumable electrode, slag protection.
-
GMAW: Continuous wire feed, inert/active gas shielding.
-
GTAW: Non-consumable tungsten electrode, inert gas shielding.
2. What factors determine the strength of an arc welded joint?
- Base metal composition, electrode selection, joint design, welding parameters.
3. Can arc welding be used to join dissimilar metals?
- Yes, but it requires special techniques and compatible filler materials.
4. What safety precautions should be taken when arc welding?
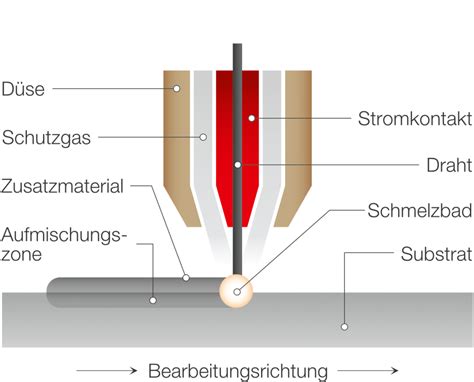
- Wear appropriate protective gear, use ground clamps, ventilate the area, and keep the workspace organized.
5. How can porosity be prevented in arc welded joints?
- Use clean electrodes and base metal, shield the weld pool, and prevent moisture contamination.
6. What is the role of flux in arc welding?
- Flux protects the weld pool from oxidation, stabilizes the arc, and removes impurities.
Conclusion
Lichtbogenschweißen is a versatile and highly effective welding technique that offers numerous advantages for joining metals. By understanding the different types of arc welding processes, selecting the appropriate electrodes, and implementing effective strategies, businesses and manufacturers can optimize their arc welding operations for increased productivity, improved weld quality, and enhanced safety. By embracing the latest advancements in welding technology, such as automation and robotic systems, users can further maximize the benefits of arc welding and remain competitive in today's demanding industrial landscape.
Call to Action
To learn more about arc welding techniques, equipment, and safety guidelines, consult with welding experts, attend industry workshops, or refer to reputable online resources. By investing in proper training and equipment, you can unlock the full potential of arc welding and achieve exceptional results in various metalworking applications.