**Thread Galling: Prevention and Mitigation Strategies for Optimal Fastener Performance**
Introduction
Thread galling is a common and costly problem encountered in countless industrial applications. This phenomenon occurs when two threaded components come into contact under high load and relative motion, causing seizure and damage to the threads. Thread galling not only compromises the integrity of the joint but also leads to downtime, increased maintenance costs, and potential safety hazards.
Understanding Thread Galling
Thread galling is a complex process that arises due to a combination of several factors:
-
High contact pressure: The high loads applied to threaded connections create intense pressure between the threads, promoting plastic deformation and metal-to-metal contact.
-
Relative motion: When threaded components rotate or slide against each other, the friction generated further exacerbates the contact pressure and promotes galling.
-
Material properties: The materials used in threaded components play a significant role in galling resistance. Soft or ductile materials are more susceptible to galling, while harder materials with high-strength properties offer better resistance.
-
Surface finish: Rough or damaged thread surfaces can create focal points for stress concentration, increasing the likelihood of galling.
-
Lubrication: Lack of lubrication between the threads can increase friction and accelerate the galling process.
Consequences of Thread Galling
Thread galling can have severe consequences for threaded connections, including:

-
Reduced joint strength: The damaged threads weaken the joint, potentially leading to premature failure.
-
Increased downtime: Galling can result in jammed fasteners that require time-consuming and expensive repairs.
-
Increased maintenance costs: Replacing damaged fasteners, cleaning threads, and applying anti-galling treatments can add significant costs to maintenance operations.
-
Safety hazards: Failed threaded connections can lead to equipment malfunction, posing potential safety risks.
Prevention and Mitigation Strategies
Preventing and mitigating thread galling is crucial for ensuring the reliability and safety of threaded connections. Here are some effective strategies:
1. Material Selection
Opting for harder and more galling-resistant materials for threaded components is a critical step. Common materials include:
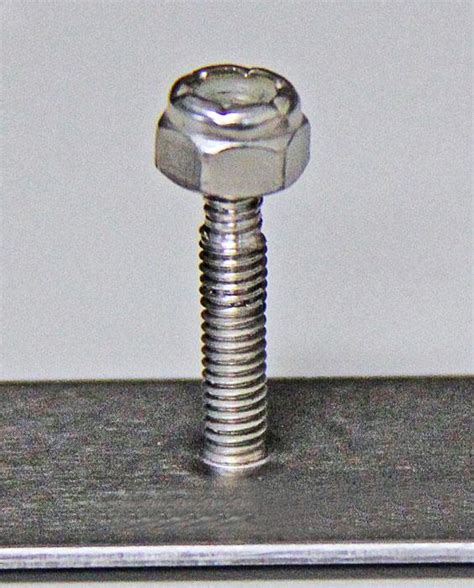
-
Stainless steel: Offers high corrosion resistance and good galling resistance, making it suitable for applications in corrosive environments.
-
Hardened carbon steel: Provides higher strength and galling resistance than standard carbon steel.
-
Coated materials: Applying coatings such as zinc, chrome, or nickel to the threads can improve surface hardness and reduce friction.
2. Surface Treatment
Improving the surface finish of the threads can reduce the risk of galling. Techniques include:
-
Polishing: Smoothing out rough surfaces eliminates potential stress concentration points.
-
Thread rolling: This process produces hardened and polished threads with improved galling resistance.
-
Deburring: Removing burrs or sharp edges prevents damage to the threads during assembly.
3. Lubrication
Applying a suitable lubricant between the threads reduces friction and prevents metal-to-metal contact. Lubricant options include:

-
Thread compounds: These pastes or liquids are specially formulated to prevent galling and enhance thread performance.
-
Dry lubricants: Solid-film lubricants such as molybdenum disulfide or graphite offer lasting protection in high-temperature applications.
-
Extreme-pressure (EP) lubricants: These lubricants are designed for heavy-duty applications and provide excellent galling protection under high loads.
4. Design Considerations
Incorporating proper design features can help prevent galling:
-
Proper thread tolerance: Maintaining appropriate thread tolerances ensures a good fit between the components, reducing the risk of excessive contact pressure.
-
Increased thread engagement: Ensuring sufficient thread engagement length distributes the load evenly, reducing the likelihood of galling.
-
Use of thread lockers: Thread lockers prevent loosening due to vibration and movement, reducing the risk of galling caused by relative motion.
5. Installation Practices
Following proper installation procedures can minimize the risk of galling:
-
Avoid cross-threading: Ensure that the threads are properly aligned before assembly.
-
Tighten gradually: Apply torque gradually, allowing the threads to engage smoothly without excessive force.
-
Use assembly tools: Use properly calibrated torque wrenches or assembly tools to achieve the recommended tightening torque.
-
Inspect threads: Regularly inspect threads for damage or wear, and perform necessary maintenance or repairs.
Economic Benefits of Preventing Thread Galling
Preventing thread galling can yield significant economic benefits for businesses and industries. These benefits include:
-
Reduced downtime: Avoiding costly repairs and downtime associated with failed threaded connections.
-
Lower maintenance costs: Minimizing the need for fastener replacement, thread cleaning, and other maintenance expenses.
-
Improved safety: Preventing equipment malfunctions and reducing safety risks related to failed threaded connections.
-
Environmental sustainability: Reducing the use of materials and energy associated with fastener replacement and repairs.
Conclusion
Thread galling is a prevalent issue that can have severe consequences for threaded connections. By understanding the causes and implementing effective prevention strategies, industries can mitigate the risks associated with galling, enhance the reliability and safety of their operations, and achieve significant economic benefits.
Tables
Table 1: Material Properties and Galling Resistance
Material |
Hardness (HRC) |
Galling Resistance |
Stainless steel (316) |
20-25 |
Moderate |
Hardened carbon steel |
30-35 |
High |
Coated materials (zinc, chrome) |
40-50 |
Excellent |
Table 2: Thread Surface Treatments and Galling
Treatment |
Surface Hardness |
Galling Resistance |
Polishing |
15-20 microns |
Moderate |
Thread rolling |
25-30 microns |
High |
Deburring |
Eliminates burrs |
Low |
Table 3: Lubricant Types and Galling Protection
Lubricant Type |
Application |
Galling Protection |
Thread compounds |
General purpose |
Moderate |
Dry lubricants |
High-temperature applications |
Excellent |
Extreme-pressure (EP) lubricants |
Heavy-duty applications |
Excellent |