Your Ultimate Guide to Air Compressors: Understanding, Selecting, and Using the Right Equipment
Introduction
An air compressor is a device that converts electrical energy into potential energy stored in compressed air. Compressed air is then used to power various industrial and home applications, from powering pneumatic tools and inflating tires to operating paint sprayers and cleaning equipment.
In this comprehensive guide, we will delve into the world of air compressors, providing you with everything you need to know to select, use, and maintain the right compressor for your specific needs. Whether you're a homeowner, contractor, or business owner, this guide will empower you with the knowledge and confidence to harness the power of compressed air.
Understanding Air Compressors
Types of Air Compressors
1. Reciprocating Compressors
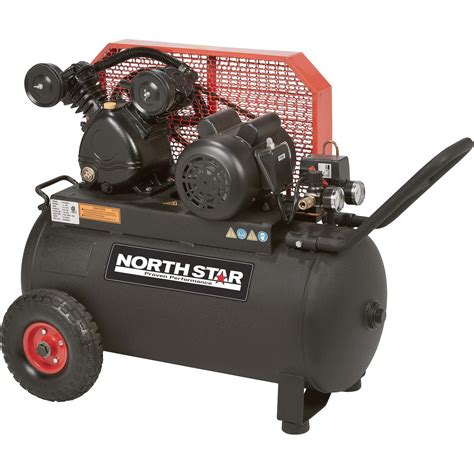
- Positive-displacement compressors that use a piston or diaphragm to compress air
- Best suited for small-scale applications with intermittent use
- Relatively noisy and produce more vibration compared to other types
2. Rotary Screw Compressors

- Positive-displacement compressors that use two intermeshing screws to compress air
- More efficient and quieter than reciprocating compressors
- Ideal for continuous or heavy-duty applications
3. Centrifugal Compressors
- Dynamic compressors that use rotating impellers to increase air velocity and pressure
- Capable of generating large volumes of compressed air at high pressures
- Most commonly used in industrial and commercial settings
Key Specifications
1. CFM (Cubic Feet per Minute)

- Measures the volume of air delivered by the compressor in a minute
- Crucial for determining the compressor's capacity to power tools and equipment
2. PSI (Pounds per Square Inch)
- Measures the pressure of the compressed air
- Higher PSI is required for more demanding applications
3. Duty Cycle
- Indicates the percentage of time the compressor can operate continuously without overheating
- Important for avoiding damage and ensuring longevity
Air Quality Considerations
-
Moisture: Compressed air can contain moisture, which can damage tools and equipment. Consider using a dryer to remove moisture.
-
Oil: Oil-lubricated compressors produce compressed air that contains oil. If oil contamination is unacceptable, use an oil-free compressor.
Selecting the Right Air Compressor
Factors to Consider
-
Application: Determine the specific tools and equipment you need to power.
-
Volume and Pressure Requirements: Calculate the CFM and PSI required for your applications.
-
Duty Cycle: Estimate the amount of time you will be using the compressor.
-
Mobility: Consider whether portability is important for your needs.
-
Budget: Establish a budget that aligns with your requirements and affordability.
Using an Air Compressor Safely
-
Follow Manufacturer's Instructions: Carefully read and adhere to the manufacturer's guidelines for operation and maintenance.
-
Ventilation: Ensure adequate ventilation to prevent the accumulation of fumes and heat.
-
Wear Safety Gear: Use ear protection and safety glasses when operating the compressor.
-
Inspect Regularly: Check the compressor regularly for any signs of damage or leaks.
-
Maintenance: Perform routine maintenance, such as oil changes and filter replacements, to extend the compressor's lifespan.
Effective Strategies for Using Your Air Compressor
-
Use the Right Size Compressor: Select a compressor that meets your specific CFM and PSI requirements.
-
Match Tools to Compressor Capacity: Avoid overloading the compressor by using tools within its rated capacity.
-
Minimize Air Leaks: Regularly inspect and repair any leaks in hoses or fittings to prevent wasted air.
-
Maximize Airflow: Use efficient hoses with large diameters to minimize pressure drop.
-
Maintain Regular Maintenance: Follow the manufacturer's recommended maintenance schedule to ensure optimal performance and longevity.
A Step-by-Step Approach to Starting and Using an Air Compressor
-
Assemble the Compressor: Connect all components, including the tank, hoses, and tools.
-
Check Oil Level: Ensure the compressor has sufficient oil for proper lubrication.
-
Turn On the Compressor: Switch the power switch to the "On" position.
-
Allow Pressure to Build: Wait for the pressure gauge to reach the desired PSI level.
-
Connect Tools and Accessories: Attach the necessary tools and accessories to the compressor's outlets.
-
Use Tools: Operate the tools and equipment according to the manufacturer's instructions.
-
Release Pressure: When finished using the compressor, turn off the power and release the pressure by opening the drain valve or using the pressure release button.
Comparing Air Compressors: Pros and Cons
Reciprocating Compressors
Pros:
* Lower initial cost
* Suitable for intermittent use
* Simple to operate
Cons:
* Noisier and more vibration
* Less efficient than other types
Rotary Screw Compressors
Pros:
* More efficient and quieter
* Longer lifespan
* Capable of continuous duty
Cons:
* Higher initial cost
* More complex to maintain
Centrifugal Compressors
Pros:
* Capable of generating large volumes of compressed air
* Suitable for high-volume applications
* Highly efficient

Cons:
* Most expensive type
* Requires specialized expertise to maintain
Frequently Asked Questions (FAQs)
1. Why Does My Air Compressor Keep Tripping the Circuit Breaker?
- Overload: The compressor is drawing too much current due to excessive demand or malfunction.
- Electrical Fault: Check for any electrical issues, such as loose connections or faulty wiring.
2. How Often Should I Change the Oil in My Air Compressor?
- Refer to the manufacturer's recommendations, typically every 500-1000 operating hours or 6-12 months.
3. What is the Difference Between CFM and SCFM?
- CFM: Measures the volume of air delivered at atmospheric pressure.
- SCFM: Measures the volume of air delivered at standard conditions (14.7 PSI and 68°F).
4. How Can I Reduce the Noise Level of My Air Compressor?
- Use noise-reducing enclosures or baffles.
- Place the compressor in a soundproofed area.
5. What is a Receiver Tank and Why Do I Need One?
- A receiver tank is a storage vessel that stores compressed air to maintain a constant air supply.
- It reduces pressure fluctuations and ensures a smooth flow of air to tools and equipment.
6. Can I Use an Air Compressor to Fill Tires?
- Yes, but use a dedicated tire inflator to regulate pressure accurately.
Tables
Table 1: Common Air Compressor Applications
Application |
CFM Requirement |
PSI Requirement |
Inflating tires |
5-10 |
80-100 |
Powering nail guns |
15-25 |
70-90 |
Spray painting |
20-35 |
50-75 |
Cleaning equipment |
30-45 |
90-120 |
Table 2: Air Compressor Maintenance Schedule
Maintenance Task |
Frequency |
Check oil level |
Weekly |
Change oil |
Every 500-1000 operating hours or 6-12 months |
Replace air filter |
Every 3-6 months |
Inspect hoses and fittings |
Regularly |
Table 3: Air Compressor Safety Tips
Safety Tip |
Purpose |
Wear safety gear |
Protect against noise and flying debris |
Ensure adequate ventilation |
Prevent accumulation of fumes and heat |
Follow manufacturer's instructions |
Operate and maintain the compressor correctly |
Inspect regularly |
Detect and fix any potential problems |
Use the right tools |
Match tools to the compressor's capacity to avoid overloading |