Washer Screw: An Essential Guide for Secure and Reliable Installations
What is a Washer Screw?
A washer screw is a mechanical fastener that combines a screw and a washer into a single unit. It consists of a helical thread that is wound around a shank, with a washer head that bears against the surface being fastened. Washer screws are widely used in various applications, offering the advantages of both screws and washers in one convenient component.
Benefits of Washer Screws
-
Prevents Overtightening: The integrated washer distributes the load applied by the screw, reducing the risk of overtightening and damage to the surface or mating components.
-
Enhanced Tightness: The large bearing surface of the washer creates greater contact area, resulting in improved tightness and resistance to loosening.
-
Vibration and Noise Reduction: The washer absorbs vibrations and dampens noise, helping to minimize operational disturbances.
-
Corrosion Resistance: Washer screws are often made of corrosion-resistant materials, such as stainless steel, making them suitable for use in harsh environments.
-
Ease of Installation: The washer screw combines two components into one, simplifying the installation process and reducing assembly time.
Types of Washer Screws
Washer screws come in various types, each designed for specific applications:
-
Hex Washer Head Screws: Feature a hexagonal head that provides ample gripping surface for tools, making them suitable for high-torque applications.
-
Pan Head Washer Screws: Have a wide, flat head with a countersunk area, allowing for flush or slightly recessed installation.
-
Button Head Washer Screws: Feature a rounded, low-profile head that sits flush with the surface, providing a clean and unobtrusive appearance.
-
Cap Head Washer Screws: Have a cylindrical head with a domed top, offering additional bearing surface and protection against tampering.
-
Bugle Head Washer Screws: Feature a tapered head that merges smoothly into the shank, creating a more aerodynamic shape for applications where wind resistance or fluid flow is a concern.
Applications of Washer Screws
Washer screws find applications in a wide range of industries and tasks, including:
-
Automotive: Securely fastening body panels, engine components, and exhaust systems.
-
Construction: Joining wood, metal, and composite materials in framing, cabinetry, and roofing.
-
Electronics: Mounting circuit boards, connecting electrical components, and securing battery terminals.
-
Industrial Machinery: Fixing guards, covers, and panels on machines, tools, and equipment.
-
Aerospace: Assemble and fasten critical components in aircraft and spacecraft, where weight reduction and reliability are paramount.
Standards and Specifications
Washer screws adhere to industry standards and specifications to ensure quality and interchangeability. Common standards include:

-
ASTM F844: Standard Specification for Stainless Steel Washer-Head Screws
-
ISO 14580: Fasteners with Washer Face - Hexagon Bolts and Screws
-
DIN 934: Hexagon Head Bolts with Flat Washer Face
Selection Criteria
Choosing the right washer screw for an application requires careful consideration of several factors:
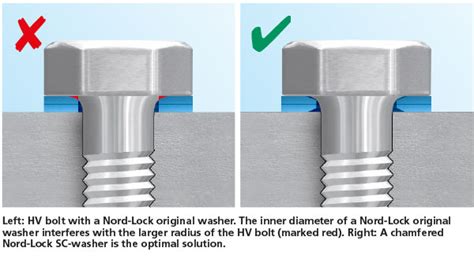
-
Material: Determine the appropriate material based on the required corrosion resistance, strength, and environmental conditions.
-
Size: Select the correct screw diameter and length based on the thickness of the materials being fastened and the desired load-bearing capacity.
-
Thread Type: Choose between coarse or fine threads to optimize holding power and resistance to vibration.
-
Head Style: Select the head style based on the required surface conditions, clearance requirements, and aesthetic preferences.
-
Drive Type: Determine the appropriate drive type (e.g., hexagon, Phillips, Torx) based on the available tools and ease of installation.
Tips and Tricks for Optimal Use
-
Use the Correct Tool: Ensure you have the appropriate tool for the washer screw head style to avoid damaging the fastener or the mating surface.
-
Apply Lubricant: Applying lubrication to the screw threads can reduce friction and prevent seizing.
-
Tighten to the Recommended Torque: Overtightening can damage the screw or the components being fastened. Use a torque wrench to ensure proper tightening.
-
Check Tightness Periodically: Monitor the tightness of washer screws over time, especially in applications subject to vibration or load changes.
-
Use High-Quality Washer Screws: Invest in washer screws from reputable manufacturers to ensure reliability and performance.
Stories and Lessons Learned
Story 1: A construction worker overtightened a washer screw while assembling a steel frame. This resulted in the screw snapping and the frame becoming unstable. The lesson learned is to follow the recommended torque specifications for washer screws to avoid such failures.
Story 2: In an automotive application, a vibration led to the loosening of washer screws on a suspension component. This caused the component to fail, resulting in a loss of control and a serious accident. The lesson learned is the importance of periodic inspections and retightening of washer screws in applications subject to vibration.

Story 3: A manufacturer of electronic devices experienced repeated failures of washer screws used to secure circuit boards. Investigation revealed that the screws were made of low-grade material and were not corrosion-resistant. The lesson learned is to use washer screws made of high-quality materials that can withstand the specific environmental conditions of the application.
Comparative Table: Washer Screw Types
Type |
Head Style |
Features |
Applications |
Hex Washer Head Screw |
Hexagonal |
High torque capacity, easy installation |
Automotive, construction, industrial machinery |
Pan Head Washer Screw |
Flat, countersunk |
Flush or recessed installation, aesthetic appeal |
Electronics, light-duty assemblies |
Button Head Washer Screw |
Rounded, low-profile |
Clean appearance, tamper resistance |
Aerospace, automotive, precision instruments |
Cap Head Washer Screw |
Cylindrical, domed |
Additional bearing surface, protection from tampering |
Industrial machinery, heavy-duty applications |
Bugle Head Washer Screw |
Tapered |
Aerodynamic shape, reduced wind resistance |
Automotive, aerospace, fluid flow applications |
Pros and Cons of Washer Screws
Pros
- Enhanced thread strength and load capacity
- Reduced risk of overtightening or stripping
- Improved vibration and noise damping
- Reduced need for separate washers
- Simplified installation
Cons
- Higher cost compared to standard screws
- May not be suitable for applications with limited space
- Can increase assembly time if a washer would have sufficed
Frequently Asked Questions (FAQs)
1. What is the purpose of a washer screw?
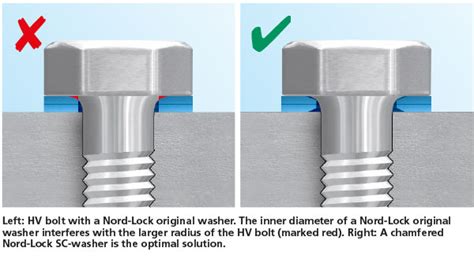
A washer screw combines a screw and a washer to provide enhanced tightening and load-bearing capacity while preventing overtightening.
2. What are the different types of washer head styles available?
Common washer head styles include hexagonal, pan head, button head, cap head, and bugle head.
3. How do I select the right washer screw?
Consider the material, size, thread type, head style, and drive type based on the specific application requirements.
4. Is it necessary to lubricate washer screws?
Applying lubrication to the screw threads can reduce friction and prevent seizing, especially in high-torque applications.
5. How often should I check the tightness of washer screws?
Periodically monitor the tightness of washer screws, especially in applications subject to vibration or load changes.
6. Can washer screws be used in harsh environments?
Yes, washer screws made of corrosion-resistant materials, such as stainless steel, can withstand harsh environments.
Additional Information
Industry Statistics:
- The global fastener market is expected to reach $126.3 billion by 2029, with washer screws accounting for a significant share.
- The construction industry is the largest consumer of washer screws, followed by automotive and electronics.
- The demand for washer screws is driven by the increasing need for secure and reliable fastening solutions in various industries.
Research and Development:
- Research is ongoing to develop washer screws with improved materials, coatings, and designs.
- Finite element analysis (FEA) is used to optimize washer screw performance and prevent failures.
- Testing and simulation are conducted to evaluate the strength, durability, and performance of washer screws in real-world applications.
Conclusion:
Washer screws are indispensable components for secure and reliable fastening in a wide range of applications. By understanding the types, benefits, and selection criteria of washer screws, you can choose the right fastener for your specific needs. By following best practices and maintaining proper maintenance, you can ensure the optimal performance and longevity of washer screws in your projects.