Enameled Wire: A Comprehensive Guide
Introduction
Enameled wire is a type of electrical wire that is coated with a thin layer of insulation, typically made of enamel. This insulation protects the wire from corrosion and other environmental factors, making it ideal for use in a wide range of applications. In this article, we will provide a comprehensive overview of enameled wire, including its properties, manufacturing process, applications, and advantages and disadvantages.
Properties of Enameled Wire
-
Electrical insulation: The enamel coating provides excellent electrical insulation, preventing short circuits and current leakage.
-
Heat resistance: Enameled wires can withstand high temperatures, making them suitable for use in harsh environments.
-
Mechanical strength: The enamel coating adds mechanical strength to the wire, making it resistant to abrasion and deformation.
-
Flexibility: Enameled wires are generally flexible, allowing for easy bending and shaping.
-
Corrosion resistance: The enamel coating protects the wire from corrosion, ensuring long-term durability.
Manufacturing Process of Enameled Wire
The manufacturing process of enameled wire involves the following steps:
-
Wire drawing: The raw wire is drawn through a series of dies to reduce its diameter.
-
Annealing: The wire is heated to a specific temperature and allowed to cool slowly, which softens it and increases its ductility.
-
Enameling: The wire is coated with a thin layer of enamel by dipping it into a heated enamel bath.
-
Curing: The enamel-coated wire is heated to cure the enamel and harden it.
-
Testing: The finished wire is tested for electrical insulation, mechanical strength, and other properties.
Applications of Enameled Wire
Enameled wire is widely used in various electrical and electronic applications, including:
-
Transformers: Enameled wire is used in the windings of transformers, which convert electrical energy between different voltage levels.
-
Electric motors: Enameled wire is used in the windings of electric motors, which convert electrical energy into mechanical energy.
-
Inductors: Enameled wire is used in the coils of inductors, which store electrical energy in a magnetic field.
-
Solenoids: Enameled wire is used in the coils of solenoids, which convert electrical energy into mechanical motion.
-
Circuit boards: Enameled wire is used to connect components on printed circuit boards.
Advantages of Enameled Wire
-
Excellent electrical insulation: Prevents short circuits and current leakage.
-
High temperature resistance: Suitable for use in harsh environments.
-
Mechanical strength: Resists abrasion and deformation.
-
Flexibility: Easy to bend and shape.
-
Durability: Protects the wire from corrosion.
Disadvantages of Enameled Wire
-
Limited flexibility: Can become brittle after repeated bending.
-
Higher cost: Compared to uncoated wire.
-
Thinner insulation: May not provide sufficient insulation for high-voltage applications.
Stories and Lessons Learned
-
Story 1: A manufacturer of transformers was experiencing frequent short circuits due to wire insulation failure. By switching to enameled wire with higher electrical insulation resistance, they were able to resolve the issue and improve the reliability of their transformers.
-
Story 2: An electric motor producer needed to use a wire that could withstand high temperatures in a harsh industrial environment. Enameled wire with excellent thermal resistance proved to be the ideal solution, allowing the motor to operate reliably under demanding conditions.
-
Lesson learned: Choosing the right type of enameled wire for specific applications is crucial for ensuring optimal performance and durability.
Comparison of Enameled Wire and Uncoated Wire
Characteristic |
Enameled Wire |
Uncoated Wire |
Electrical insulation |
Excellent |
Poor |
Heat resistance |
High |
Low |
Mechanical strength |
High |
Low |
Flexibility |
Good |
Excellent |
Corrosion resistance |
Good |
Poor |
Cost |
Higher |
Lower |
Frequently Asked Questions (FAQs)
-
What is the difference between enamel wire and magnet wire? Magnet wire is a specific type of enameled wire that is specifically designed for use in windings of transformers and electric motors.
-
What is the temperature range for enameled wire? The temperature range for enameled wire varies depending on the type of enamel used. Generally, enameled wires can withstand temperatures up to 200°C (392°F).
-
Can enameled wire be soldered? Yes, enameled wire can be soldered, but the enamel coating must be removed from the area to be soldered.
-
What is the insulation resistance of enameled wire? The insulation resistance of enameled wire is typically in the megohms per meter range.
-
Is enameled wire available in different colors? Yes, enameled wires are available in a variety of colors for easier identification and organization.
-
What is the chemical composition of enamel coating? Enamel coatings can be made from different materials, including polyurethane, polyimide, and polyester.
Call to Action
If you are looking for a high-quality electrical wire with excellent insulation, temperature resistance, and durability, enameled wire is an ideal choice. Contact a reputable wire manufacturer today to discuss your specific needs and find the right enameled wire solution for your application.
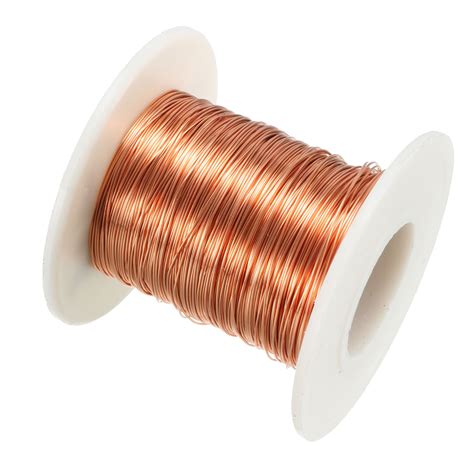